
■Concept
A car's suspension is basically a coil spring made from a small metal bar. The technology and quality of the material used to coil this metal bar have a huge impact on the effectiveness of the suspension system. Coiling this high-quality alloy requires expertise in both production and development methods. Precisely because we work with raw materials it is essential that we have the know-how when it comes to ride height, riding comfort and durability. Our experience in the field and our position as the No.1 seller of suspension coils have allowed us to carry out research and development and to perfect the technology required producing our top quality suspension coils.
■Line-up
・Down
Thanks to the knowledge we have gained through many years of developing coil technology we have been able to achieve maximum compression of our springs to get your car as low as possible. We have been able to achieve a low ride height and get that stylish look without sacrificing handling or ride comfort. When you drive with this suspension you will feel its quality.・Super Down
The Super Down suspension gives the maximum drop in vehicle ride height. This suspension is designed for demonstration and show cars and does not give sufficient clearance to drive on the public roads.・Hard Down
The Hard Down suspension combines a drop in ride height and an increased spring rate for aggressive driving on the track.・Half Down/Hi-Road
Here at TMC we aim to provide suspension that can be tailored to each car.・Ti2000 Straight
The Ti2000 straight spring is for coilover.・Helper spring
Details for helper spring.・Coil Spring Tube
Cracking noise may occur from an irregular pitch of spring for some model. The Coil Spring Tube will be efficient to reduce this noise.■Unique material for each series
・RS*R series
Thanks to RS*R's position as the No.1 seller of aftermarket suspension kits we are able to offer a wide range of products at the lowest possible price.At the forefront of technology RS*R suspension uses new and improved materials to give maximum durability. All the RS*R series comes with a 3-year/50,000km limited warranty.
※Current series:RS*R Down RS*R Super Down RS*R Hard Down
・Ti2000 series
The Titanium alloy we use in manufacturing is ideal for suspension kits and is extremely durable. The material is of the highest quality (and comes with an unlimited warranty).The Ti2000 gives the driver the maximum drop in ride height without compromising riding comfort. The driver will notice the difference.
※Current series:Ti2000 Down Ti2000 Half Down Ti2000 Super Down Ti2000 Hard Down Ti2000 Hi-Road Ti2000 Straight
TMC's original material
Material | C (Carbon) | Si (Silicon) | Mn (Manganese) | Cu (Copper) |
Cr (Chromium) | Ni (Nickel) | V (Vanadium) | Ti (Titanium) |
---|---|---|---|---|---|---|---|---|
Ti2000 | 0.40 | 1.80 | 0.18 | 0.25 | 1.05 | 0.52 | 0.18 | Trade secret |
Company D SAE9254V | 0.54 | 1.37 | 0.72 | - | 0.71 | - | 0.002 | - |
Company S SAE9254V | 0.56 | 1.39 | 0.70 | - | 0.71 | - | 0.054 | - |
The original material we use at TMC is what makes our suspension kits superior. The Ti2000 spring is made with a unique combination of Chromium and Nickel to give extra durability and an exceptional resistance to corrosion.
Many of our competitors use the material SAE9254V in their production, which is a low alloy steel with added Vanadium. Although the added Vanadium improves durability, when the spring is compressed and put under high stress, the corrosion and delayed fracture resistance is weakened.
However, we TMC succeeded to create more durable material under high stress against corrosion and delayed fracture by adding Chromium, Nickel and Titanium without sacrificing the performance that the material originally has.
The effect of Titanium
Grain boundary, which constitutes the spring, is weakened its bonding power by nitrogen. By adding Titanium to the spring, nitrogen will not stay at grain boundary because it forms nitrogen trap. This will prevent the deterioration of bonding power.▼ If Titanium is not included... ▼

This is metal crystal.
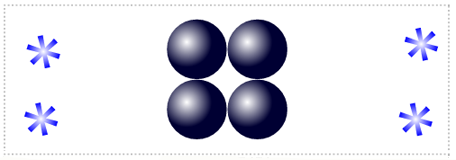
If nitrogen comes into the crystals,
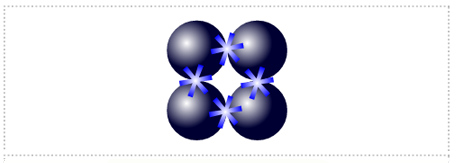
it will stay between grain boundary and destroy the crystals.
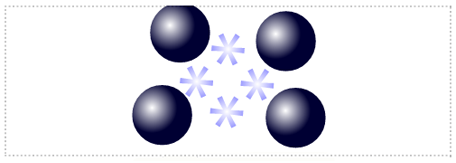
The destruction of the crystals will cause the deterioration or breakage of the spring.
▼ If Titanium is included... ▼
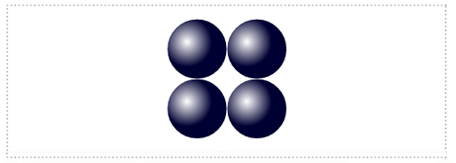
This is metal crystal.
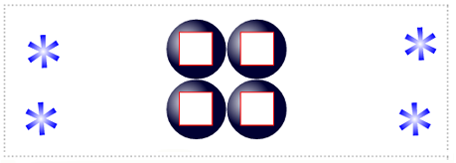
Titanium is added here,
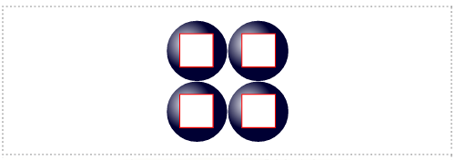
Nitrogen trap is formed.
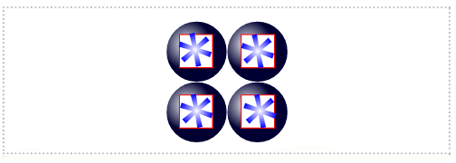
This trap absorbs the nitrogen when it comes in so it will be able to maintain the stable status.
High-frequency induction furnace
One important factor in the structure of the metal compound is the balance between heating time and heating temperature. If the heating time is short the crystals will bind tightly and form a compound that is resistant to corrosive elements such as hydrogen.▼ Oil furnace (up to now) ▼
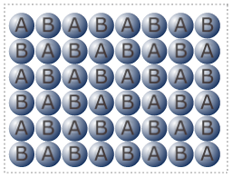
Heating,
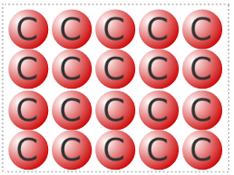
As the metal compound is expanded due to long heating, bonding becomes fragile.
▼ High-frequency induction furnace ▼
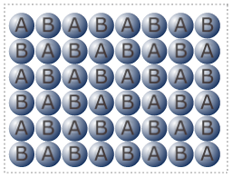
Heating,
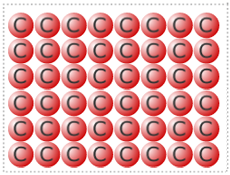
With short heating at high temperature, the metal compound becomes minute and it will generate the strong material.
In making the material for the Ti2000 coil a high-frequency induction furnace is used in order to reduce the time needed to forge the metal. The oil furnace which was previously used to forge the metal took 900 seconds whereas the high-frequency induction furnace which is currently used takes just 8-16 seconds. This difference has a huge influence on the strength and durability of the compound. Currently the Ti2000 is the only suspension coil using this technology.
The numerical value of the Ti2000
The radar chart below shows five key factors in determining the performance and durability of a vehicle suspension. From this chart you can clearly see that the new Ti2000 suspension is superior to other suspension kits in every way.
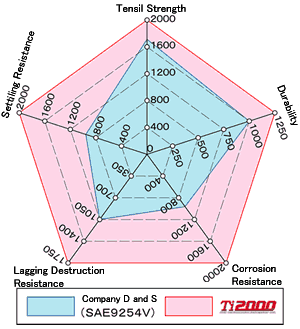
Paint
The Ti2000 uses paint which is a 2-part epoxy coating. Epoxy coatings have excellent resistance against corrosion and their protective coating and polyester finish are great protection against color fade. Using this hybrid polyester epoxy paint brings the Ti2000's performance to the limit!
Manufacturing process
How is the Ti2000 spring made? High-quality materials show their real value with high technology. Let us introduce the manufacturing process of the Ti2000. ▼ 11 manufacturing processes ▼ 1. Material inspection
2.Taper rolling
3.Heating:It was difficult to control the temperature of the heavy oil, but high-frequency induction furnace by electromagnetic induction heating enabled us to maintain the material at a constant temperature.
4.Coiling
5.Hardening
6.Tempering
7.Hot setting
8.Hot shot peening:By hot shot peening, surface stress is penetrated more inside and at the same time residual stress is enhanced, which extend the maximum stress and stroke.
9.Cold setting
10.The low temperature powder coating:By hot setting, hot shot peening and low temperature powder coating, we drastically succeeded to enhance the potential power that we hadn't been able to do so.
11.Load test
Weight
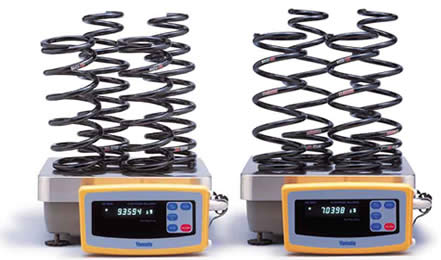
Due to the new materials used in the Ti2000 we have been able to make a highly durable suspension coil with a smaller diameter and less spring coils. Because of this, it has become possible to reduce the weight by more than 2kg. For example, the standard suspension kits(four coils) used in the Altezza SXE10 have a weight of 9.3594kg whereas the Ti2000(four coils) weighs only 7.0398kg. That is a 2.3196kg or 24.7% difference in weight. This reduction makes a noticeable difference in driving performance. That is a 2.3196kg or 24.7% difference in weight. This reduction makes a noticeable difference in driving performance.